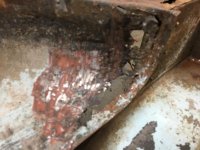
This shows the damage to the driver side rear inner wing after the patch was removed from the inside and the goop that covered the outside.
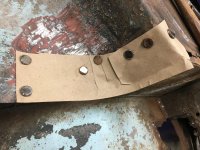
This shows the template with the over laps in the curve indicating that it needed to be shrunk in this area. This turned out to be a mistake. After 2 attempt to shrink this area it only yielded a beat up piece of sheetmetal. There is no bowl shape to this area, it is curved but is flat if that makes since. I took a larger piece of paper and turned it perpendicular to the curved area and it fit with very minor wrinkling. I cut a larger piece of sheetmetal and drew lines on it to represent the curve. put it in the english wheel with a rubber band on the top wheel so that it only curved the metal in one direction without stretching the metal. That put me on the right track.
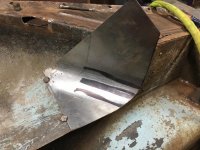
The piece fit in nicely enough I could do an initial scribe line along the bottom of the inner wing and cut that excess off. The lines show the direction of the curve.
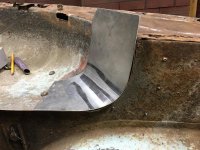
This shows a little more whittled off the repair piece. I do not think I could have made a template cut the piece out and formed it to fit. I had to form the curve and then start removing excess a little at a time as the piece fits a little better each time.
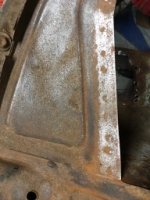
This is how I find the spot welds to drill them out to remove pieces to be repaired. A piece of 80 grit sand paper sand over the spot welds and this will leave a dot where the spot weld is either paint or rust but it makes them easier to find. I use a 3/8 " pilot point drill that drills the spot weld and the outer area helps to keep from drilling thru the panel I am trying not to damage. Some times I end up using a 3/8" ball end rotary burr that also works well if you have one side of the spot weld that is still holding on.
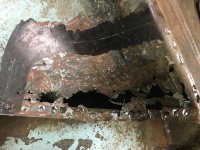
Spot welds being drilled out trying not to disturb the boot floor flange that the repair will join. The boot floor will be replaced later but for now I need it to get this repair correct. The area that will be cut out has been scribed. I use a magnum sharpie to darken the area so I can see the scribe line better.
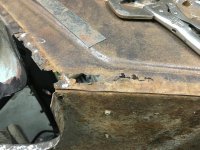
The damage has been rough cut leaving about 1/4" to be cut once the flanges under the repair can be repaired.The cut out area is not easy to see in this picture . I will have a better shot in the next post . This is the lower part of the boot side wall. An easy repair that will be cut out and a new piece welded in. Hope the long post are not too boring. This repair helped me to see that you can not get locked into a train of thought, if it is not working try another approach. Frank